Light Scattering Analysis for the Optimization of Optical Fabrication
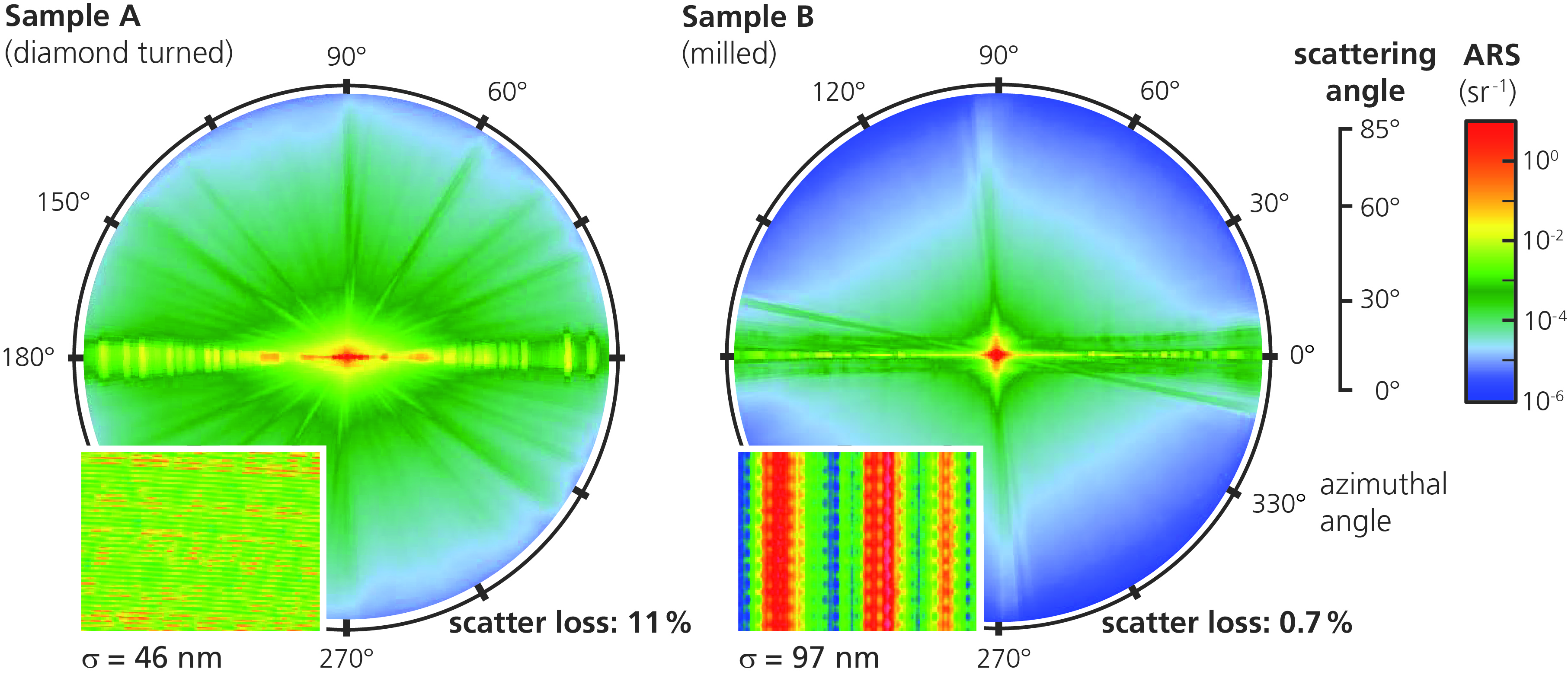
The fabrication of optical components with a surface and material quality that is adapted to the application requirements results in time consuming and expensive process chains. On the one hand, insufficient qualities of surface and material increase light scattering losses, decrease image quality, and increase stray light problems. On the other hand, specifications that are too tight lead to unnecessary process and fabrication expenses. Especially for high volume optics, a tailored optimization of the light scattering performance only in the application relevant region of scattering angles often allows relaxed specifications in other regions. This allows either a reduction in production costs while the application relevant quality stays the same, or drastically improving the optical performance with even small changes in the fabrication process. In order to tailor the fabrication processes to the application relevant specifications, a detailed understanding of the optical characteristic is mandatory, especially regarding the relationship between light scattering and surface and material properties.