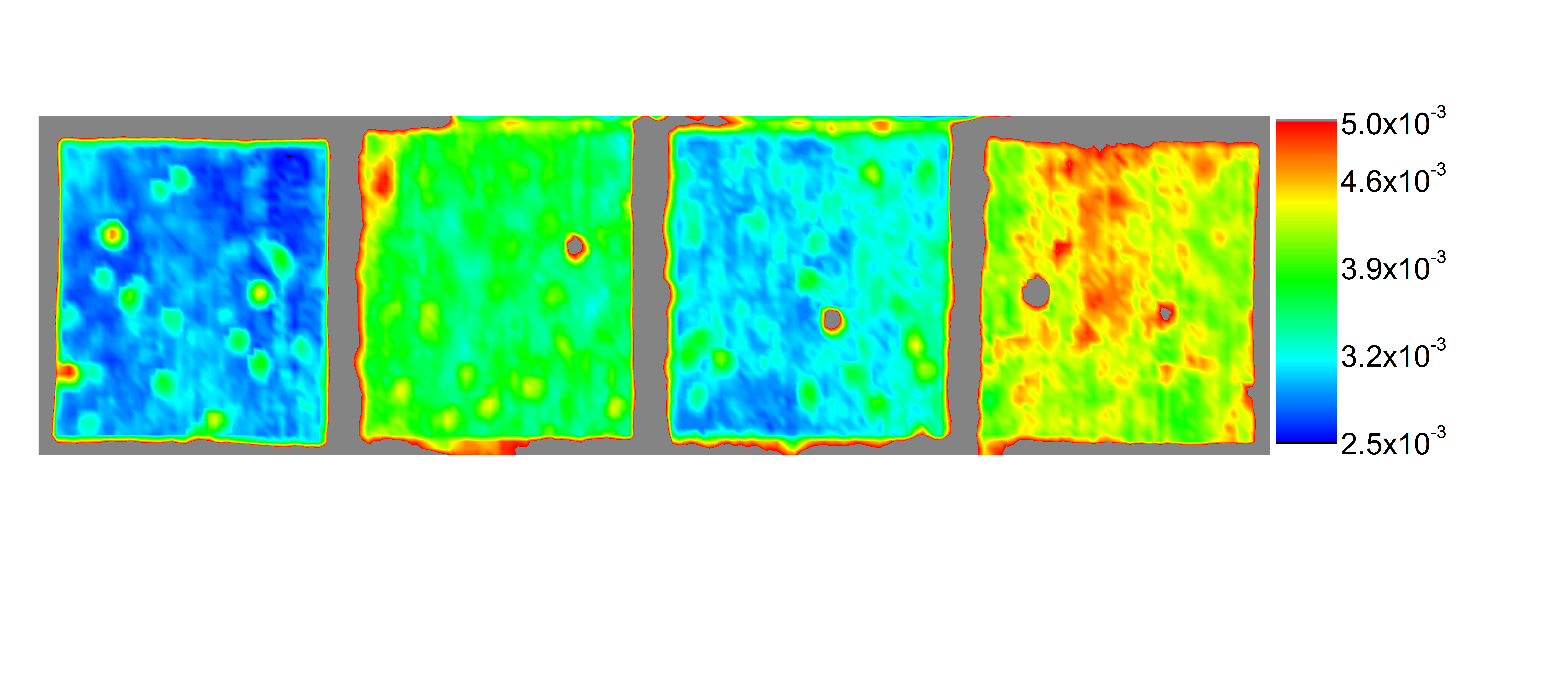
For the characterization of surface imperfections such as roughness and defects, light scattering techniques have the advantages of being flexible, robust, non-contact, and highly sensitive. In particular, the characterization of optical surfaces and components usually requires highly sensitive, but complex, goniometer systems. However, with increasing size and complexity of the samples, these instruments reach their limitations in particular in sample handling.
In addition to goniometer based light scattering instruments, highly sensitive and compact light scattering sensors have been developed at Fraunhofer IOF in recent years. These sensors combine the advantages of light scattering measurements with in-line capabilities and have even been implemented into manufacturing machines. Analysis methods specifically developed for this approach provide links between the angle resolved scattering (BRDF) results and the structural properties of optical components like surface roughness or homogeneity. The measurement results are comparable to other approaches such as white light interferometry, but are acquired more easily and faster. In addition, direct information on the scattering properties is obtained.
The compact light scattering sensor has now been combined with a collaborative and interactive robot in order to fully exploit its potential. This system and novel software modules enable the sensor to be automatically traced over complex shaped surfaces with diameters of up to 1 m to map the entire surface e.g. for roughness. On the other hand, the collaborative robot with its integrated protective mechanisms keeps the safety efforts minimal and would even enable a mobile application of the entire system. The collaborative operation also allows positioning of the sensor at selected sample positions by hand. Thereby the sensor position is tracked and the results are registered in a surface map.
Authors: Tobias Herffurth, Sven Schröder